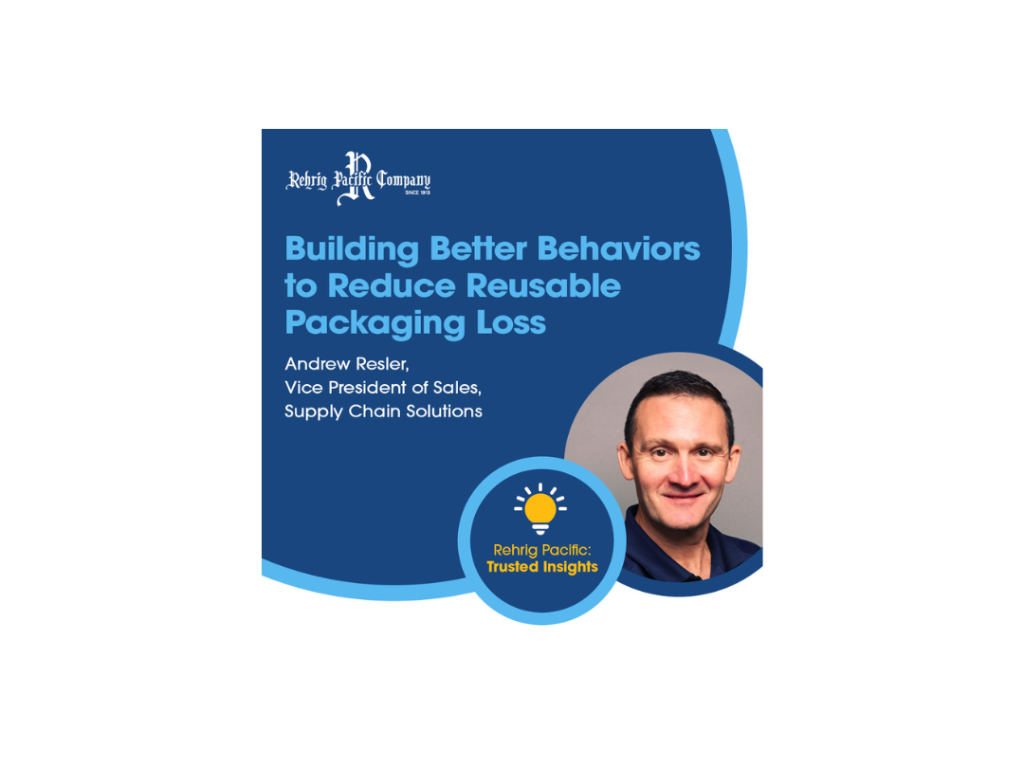
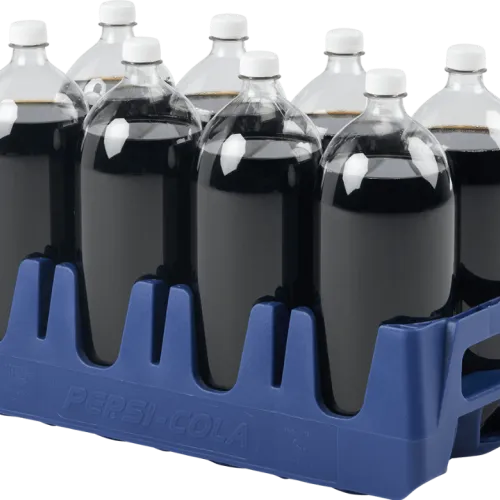
So, what does this have to do with reusable packaging loss? The same strategy that helps you keep track of your keys can be scaled to drive positive habits and behaviors that ensure your reusable assets (pallets, bins, totes, crates, etc.) remain where you need them. While we won’t use bowls and racks to manage reusable assets, we can apply the same basic principles to create awareness, set expectations, and foster habits that yield predictable outcomes. Let’s explore a few practices that have proven effective in creating more reliable systems.
Create Awareness
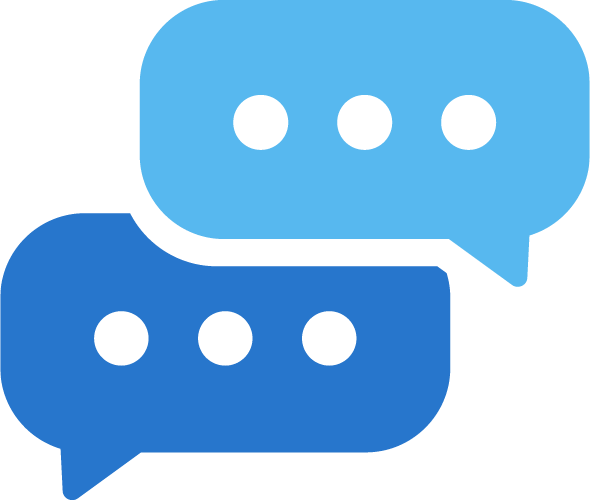
Visuals
Develop Training Programs
As with any core process, some level of training is required to develop the skills and awareness necessary to perform tasks effectively. The good news is you likely already have role-specific training in place, so most of the groundwork is done. When evaluating your supply chain for reusable packaging, pay attention to what each role needs to know to achieve your desired performance. Incorporate this into your existing training programs to ensure your team is set up for success.
Audit and Reinforce
We’ve all heard the saying, “What gets measured, gets done.” It’s a simple yet powerful idea. After creating awareness, establishing visuals, and training your team, take the time to observe the system in action. Recognize and reinforce positive behaviors, coach where necessary, and solicit feedback. This gives you the opportunity to refine your Plan, Do, Check, Act (PDCA) cycle and address any areas that are not meeting expectations.
Focus on the “Last Mile”
When it comes to developing these behaviors, the critical touchpoints often lie between your distribution center, drivers, and retail partners—what we call the “last mile.” Simple communication, visuals, and expectation setting in the last mile are key to completing your reusable loop. Believe it or not, sometimes drivers and store owners are unaware that reusable packaging needs to be returned. Never assume. Make sure expectations are clearly set and consistently followed up on to keep your assets moving.
By applying these basic steps, you can positively influence all aspects of your supply chain performance, from loss rates, dwell times, to overall financials. Just like with your keys, a simple system and consistent follow-through can yield significant results and reduce frustration. If you’re unsure where or how to start, rely on Rehrig Pacific! We are your trusted supply chain partners, committed to delivering solutions that move your business forward.
Author: Andrew Resler, Vice President of Sales, Supply Chain Solutions